Background
Introduction to our project
The purpose of our project is to investigate the effect of filling, storage and discharge of the contents of a thin-walled steel silo through an eccentric hopper .
The effects of concentric discharge through a conical right-circular hopper which, along with the silo barrel itself, is axisymmetric, are relatively well-documented (Rotter, 2001), and various standard results for the pressure distributions (e.g. Janssen theory) and stress resultants (e.g. bending and membrane theories) have been derived. Unfortunately, the effects of discharge through an eccentric hopper are not yet well understood. This is due to the non-linearity of the problem as a result of the large warping and bending stresses (Rotter, 1987a) which, from observation, are seen to be introduced into the hopper wall making modelling and derivation of governing formulae extremely difficult.
One may ask: "Why is this at all important? Can’t one not simply build symmetrical silos with equally symmetrical hoppers and not take the risk of having this spectacular failure?". The answer is that, yes, one could continue doing so, but there are some practical problems associated with this which make the use of eccentric hoppers quite tempting. The lack of prior research in this field makes people reluctant to risk building such hoppers, and if they do then it is usually on a very small scale. The full power of the eccentric hopper is thus yet to be unleashed...
But first, some clarification of basic silo components, best done, as always, by a diagram (after Rotter, 2001).
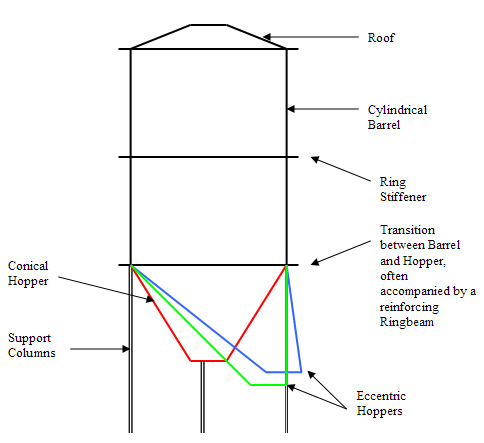
Fig. 1
Concentric Vs Eccentric Discharge top Δ
One may see already that the main advantage of the eccentric hopper is that it allows the discharge of the silo contents to a much more easily-accessible location away from the silo cross-sectional area. For conical hoppers, discharge occurs directly under the hopper, which implies that some receiving body (i.e. trucks, cisterns, conveyor belts, skips, train carts etc.) is also present directly under it, along with some means of its removal from under the silo. This puts the structure of the silo at significant risk, and any vehicle needing to situate itself directly under the hopper between the support columns introduces the possibility of impact with them.
For small silos, this may not even be possible and extra measures such as a mechanised conveyor system would need to be installed, of course, at extra cost. For medium sized silos, the supports may be far enough apart to allow some truck to come in, but only just. They would be too far apart not to justify any conveyor system, but close enough to allow the truck to hit them at the slightest miscalculation by the driver. For large silos, the sheer size of it means a catastrophic failure should one support fail, and large economic and possibly human losses. Evidently, no conical hopper is without its logistical problems.
In agriculture, small silos with eccentric discharge are used as they are convenient for loaders to be filled adjacent to the silo, thus reducing the need for the installation of auger type conveyance systems. Large scale silos with eccentric hoppers are not widely used in practice, primarily because the theory behind their design is extremely complex and not yet fully understood (Rotter, 2001). Also, since large concentric hoppers are generally big enough for collecting trucks to drive under them, the very need for large eccentric hoppers is reduced and people do not see why they should risk building them.
Therefore, the presence of the standard concentric alternative to eccentric hoppers for large-scale silos, and the lack of any significant impact on structural integrity for small-scale silos, means that there has not been a lot of incentive to research this area in greater detail. But it would be a shame to continue to leave this aspect of silo theory in the dark, as it is an interesting little problem, really, with many other potential applications, and we shall attempt to contribute to its promotion in our thesis work.
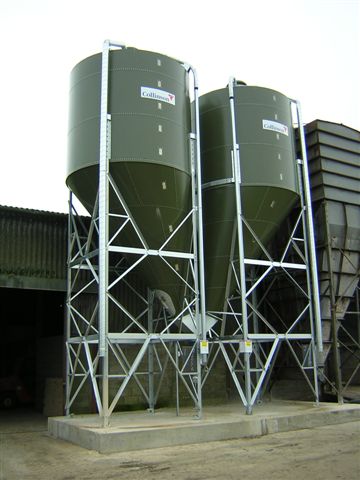
Fig. 2 - Eccentric Hoppers discharging into single conveyor
(Photo reproduced courtesy of Collinson Plc, www.collinson.co.uk)
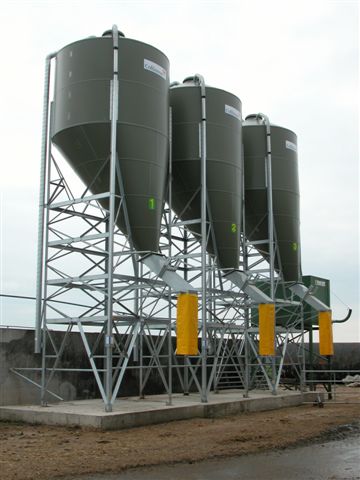
Fig. 3 - Eccentric Silos for drive along discharge
(Photo reproduced courtesy of Collinson Plc, www.collinson.co.uk)